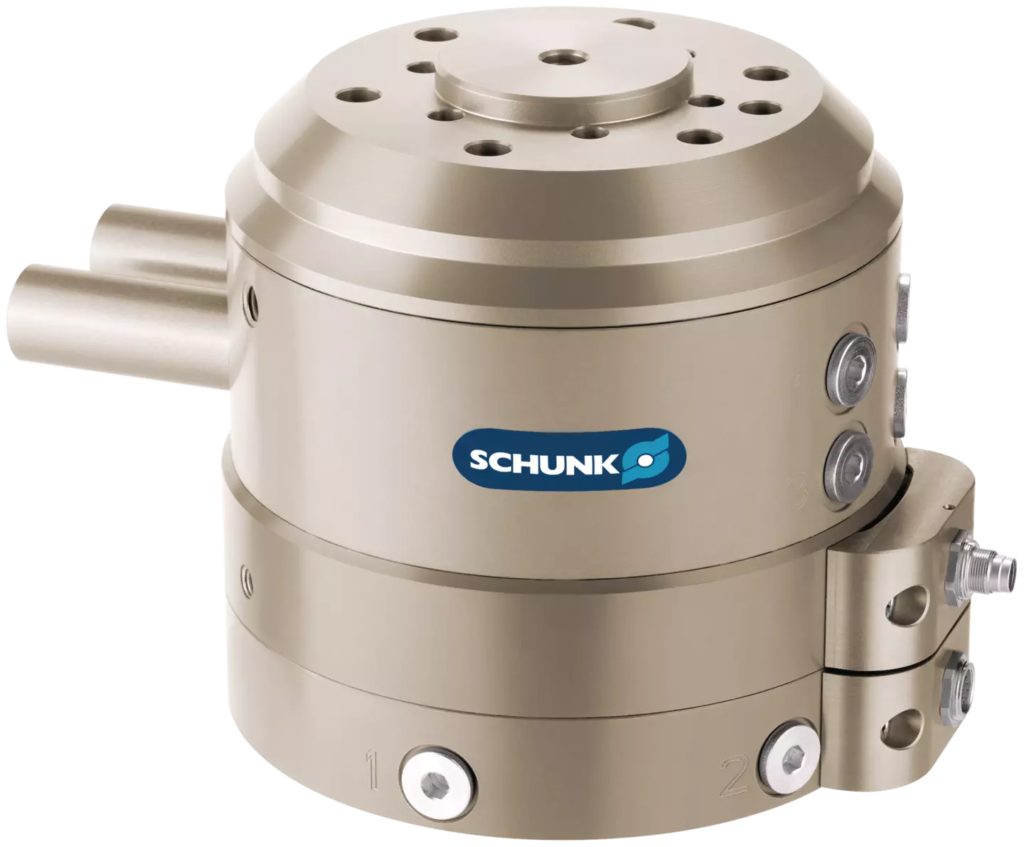
Vacuum rotary feedthroughs play a crucial role in maintaining the integrity of vacuum systems by allowing the transfer of mechanical motion or fluids across a vacuum barrier. These ingenious devices enable the rotation of shafts, probes, or components inside a vacuum chamber without compromising the vacuum level.
In this comprehensive guide, we delve into the essence of vacuum rotary feedthroughs, their types, functions, applications, and how they are essential components in various vacuum systems.
Understanding Vacuum Rotary Feedthrough
1. Function and Principle:
A vacuum rotary feedthrough, also known as a vacuum rotary joint, is designed to transmit mechanical motion or fluids from outside a vacuum chamber to the inside, or vice versa, while maintaining a vacuum-tight seal. This is achieved through a combination of precision engineering and sealing mechanisms. The feedthrough typically consists of a rotating shaft, bearings, seals, and a vacuum flange. The rotating shaft passes through the vacuum chamber wall via a hermetic seal, allowing controlled rotation without introducing contaminants or compromising the vacuum environment.
2. Sealing Technologies:
Various sealing technologies are employed in vacuum rotary feedthroughs to ensure a reliable vacuum seal while allowing smooth rotation. Common sealing methods include:
3. Labyrinth Seals: These seals use a series of interlocking grooves to create a tortuous path for gas molecules, preventing them from escaping the vacuum chamber.
4. Magnetic Fluid Seals: These innovative seals utilize a magnetic fluid or ferrofluid to create a dynamic, self-healing seal around the rotating shaft. The seal adjusts automatically to changes in pressure or temperature, ensuring continuous vacuum integrity.
5. Mechanical Face Seals: Also known as mechanical or dry contact seals, these seals use flat faces pressed together to create a seal. They are effective for high-vacuum applications and offer low friction for smooth rotation.
6. Bellows Seals: Bellows, or accordion-like structures, provide flexibility for the rotating shaft while maintaining a vacuum-tight seal. They are ideal for applications with angular or axial movement.
Types of Vacuum Rotary Feedthroughs
- Single-Passage Feedthroughs:
These feedthroughs consist of a single rotating shaft passing through the vacuum chamber wall. They are suitable for simple applications requiring only one connection point, such as sample manipulation or probe positioning.
- Multi-Passage Feedthroughs:
Multi-passage feedthroughs feature multiple rotating shafts or channels, allowing the transmission of several signals, fluids, or gases simultaneously. They are used in complex systems requiring multiple connections, such as semiconductor manufacturing or research laboratories.
- Electric Feedthroughs:
Electric rotary feedthroughs incorporate electrical contacts within the rotating shaft, enabling the transfer of electrical signals or power across the vacuum barrier. They are commonly used for applications such as heating elements, sensors, or motor control inside vacuum chambers.
- Pneumatic or Hydraulic Feedthroughs:
These feedthroughs utilize pneumatic or hydraulic mechanisms to transmit fluids or gases across the vacuum seal. They are employed in systems requiring controlled pressure or flow of fluids, such as vacuum deposition processes or material handling.
Applications of Vacuum Rotary Feedthroughs
- Thin Film Deposition:
In vacuum coating processes such as sputtering or thermal evaporation, rotary feedthroughs are used to manipulate substrate holders, mask assemblies, or deposition sources inside the vacuum chamber.
- Semiconductor Manufacturing:
Vacuum rotary feedthroughs play a critical role in semiconductor fabrication processes, enabling the precise positioning of wafers, probes, or process chambers in vacuum environments.
- Research and Instrumentation:
Scientific research facilities and laboratories use rotary feedthroughs for experimental setups, beamlines, spectroscopy, or sample manipulation inside vacuum chambers.
- Material Processing:
Vacuum rotary feedthroughs are employed in material processing applications such as crystal growth, metallurgy, or powder handling inside controlled vacuum environments.
- Space Simulation:
For space simulation chambers or testing facilities, rotary feedthroughs are used to simulate the vacuum conditions of space and test spacecraft components or materials.
How to Use Rotary Vane Vacuum Pump: A Step-by-Step Guide
- Installation:
- Start by ensuring the vacuum pump is placed on a stable, level surface with ample ventilation.
- Connect the pump inlet to the vacuum chamber or system using vacuum tubing and appropriate fittings.
- Connect the pump outlet to a suitable exhaust or venting system to release gases and vapors.
- Power Connection:
- Plug the vacuum pump into a compatible power source, ensuring the voltage and current requirements match.
- Check the power cord and connections for any damage or loose connections before powering on.
- Startup Procedure:
- Turn on the main power switch of the vacuum pump.
- Allow the pump to run for a few minutes to reach operating temperature and stabilize.
- Monitor the pump’s pressure gauge or vacuum gauge to ensure it reaches the desired vacuum level.
- Adjusting Vacuum Levels:
- Rotary vane vacuum pumps often feature adjustable pressure or vacuum settings.
- Use the pump’s control panel or knobs to adjust the vacuum level as needed for the specific application.
- Refer to the pump’s user manual for guidance on optimal vacuum levels and settings.
- Monitoring and Maintenance:
- Regularly monitor the pump’s performance, including vacuum levels, noise levels, and temperature.
- Check for any leaks or abnormal vibrations that may indicate a problem.
- Perform routine maintenance tasks such as oil changes, filter replacements, and lubrication as per the manufacturer’s recommendations.
- Shutdown Procedure:
- When the vacuum process is complete or the system is no longer in use, follow the proper shutdown procedure.
- Turn off the main power switch of the vacuum pump.
- Close any valves or connections to isolate the vacuum chamber or system.
- Allow the pump to cool down before disconnecting any tubing or fittings.
Advantages of Rotary Vane Vacuum Pump
- Efficient Operation:
- Rotary vane vacuum pumps are known for their high efficiency in creating vacuum levels suitable for a wide range of applications.
- They offer quick evacuation times and reliable performance, making them ideal for industrial and scientific use.
- Compact Design:
- These pumps are relatively compact and space-efficient, making them suitable for installations where space is limited.
- They can be easily integrated into existing vacuum systems or setups without requiring extensive modifications.
- Low Noise and Vibration:
- Rotary vane vacuum pumps operate with minimal noise and vibration, creating a quiet working environment.
- This feature is particularly beneficial for laboratories, research facilities, and industrial settings where noise levels must be kept to a minimum.
- Versatile Applications:
- Rotary vane vacuum pumps are versatile and can be used in a wide range of applications, from vacuum drying and filtration to vacuum packaging and degassing.
- They are suitable for both rough vacuum and medium vacuum processes, providing flexibility in use.
- Reliable Performance:
- With proper maintenance and care, rotary vane vacuum pumps offer reliable, long-lasting performance.
- They are robustly built and designed for continuous operation, minimizing downtime and maintenance costs.
Conclusion
Vacuum rotary feedthroughs and rotary vane vacuum pumps are integral components of vacuum systems, enabling precise control, transmission of motion, and maintenance of vacuum levels. Vacuum rotary feedthroughs facilitate the manipulation of objects, probes, or components inside vacuum chambers without compromising the vacuum environment.